

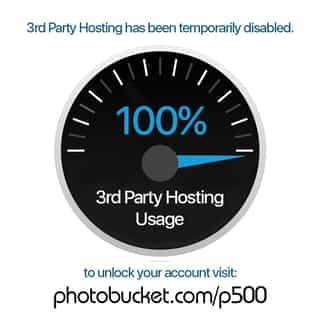
On Solidworks, your only option is to suck it up, spend hours trying to make the tree more efficient, or worst case, remodelling the entire part to be more efficient. What if your feature tree is starting to get complicated, perhaps over 150 features, and you're experimenting with different forms and you're starting to see slower rebuild performance. Let me start with a few practical examples. As an experienced CAD user, coming into NX was one mind-blowing realisation after the next - that everything I knew about modelling was wrong. NX on the other hand, has dozens of these tools, each more dizzyingly powerful than the last.

Solidworks actually does have a pitifully small number of them, 'move face' and 'delete face', which it actually had to licence from Siemens to even include. Siemens holds many patents for these tools, which is why you don't often see them anywhere else. But it is infinitely more powerful, because if you choose to, you can bypass it completely because of a suite of tools known as direct editing tools. Who needs a feature tree? Modelling in NX Let's jump straight into how you can model in NX. The only way I can explain this is by directly comparing to a better system. But if any part of your design is still fluid or experimental, or liable to change significantly, SW is hopeless and clunky. If you already know, in a finite way what your part has to look like and achieve, then SW is an efficient and capable system. Let's call it my personal philosophy on modeling. But before I continue, I will offer up a disclaimer, the approach I'm about to describe won't be for everyone.
#Siemens nx for mac software#
A majority of your time is spent thinking about strategies to prevent the software failing, instead of focusing on the design. As a student, I just thought this was the way CAD was, and that it was my responsibility to shepherd and manage a temperamental feature tree that could fall over at any moment. You could spend hours just getting back to where you were before. And god forbid if you want to go back and make significant changes in the tree. Let's be honest, how much of your time in SW is spent fixing a broken feature tree? I would argue up to 20% of an entire project can be spent rebuilding and fixing broken features. And it's true, in SW this is important because if you don't, the whole tree can break randomly if a sketch becomes undefined and conflicts with future features.
#Siemens nx for mac how to#
When being taught how to model in SW, my teachers went to great lengths to make sure we fully constrained every sketch. It's all about managing the feature tree and making sure it is efficient and well built. It's parametric solid modeling, capably done. Now to go into a bit more detail about what SW is good at, and what makes it unique. A lot of businesses use SW, so it's a useful tool to have under your belt, but at some point if you're serious about CAD work you're going to have to step up. I know this might sound like a diss, but it's not. Having said that, a HUGE swathe of mid and low-tier companies use SW. No self-respecting top-tier design company uses SW. Off the top of my head, Apple, Dyson and Mercedes all use Alias and NX for different stages in the design process. To give you some perspective, none of the big serious design companies use SW. For that, you have to step up to Alias (for A-surface modeling), CATIA or NX. SW simply doesn't have the capability to design a car, or many other objects. If you don't know what those things are, I might cover them in more detail in another article, but for now - it's basically the difference between the surfacing seen on a poorly designed hair dryer versus the smooth, flawless curves on a Mercedes.

It is not designed for class-A surfacing or critical curve control. It is designed to make simple, solid body objects and to make functional, highly controlled assemblies with those parts. The devil you know is better than the devil you don't.įrom an industry perspective, SW is an entry level CAD system. I think this is the default position of a lot of SW users. A lot of my peers complained about rebuild times and features that would fail for inexplicable reasons, but I often was able to find a way around these issues and would defend it often because I hadn't used anything else. This is the system I learnt CAD on, and when I was using it, I loved it. Not because it was good, but because of an entrenched user base and aggressive sales. 10 years ago, Solidworks cornered the education and small business markets.
